Table of Contents
According to the latest report from the market research firm Technavio, the global laser welding machine market is witnessing exciting prospects for future development. From 2023 to 2027, the market is expected to grow at a compound annual growth rate (CAGR) of 5.24%, with the market size projected to increase by $4.58 billion. This expansion is driven by multiple factors, including the growing demand in sectors such as new energy vehicles, lithium batteries, semiconductors, and emerging markets. Additionally, advancements in laser power and decreasing laser equipment prices have contributed to the increased adoption of laser welding machines across various industries. Furthermore, the widespread adoption of welding robots and the significant advantages of laser welding over traditional welding methods have further fueled the expansion of the market.
Multiple Advantages of Laser Welding

Laser technology stands out in various industrial applications due to its non-contact processing, high precision, flexibility, efficiency, automation, and adaptability. The laser welding machine market can be divided into submarkets based on the type of laser source, including fiber laser, solid-state laser, and carbon dioxide laser. Fiber laser welding machines, for instance, are used for joining various materials and possess characteristics such as minimal heat generation, which prevents damage to heat-sensitive materials, and high efficiency. This technology is versatile and offers several advantages, such as diverse fiber welding methods, small weld seams, extensive applications, low maintenance costs, and environmental friendliness.
Laser Welding in the Automotive Sector
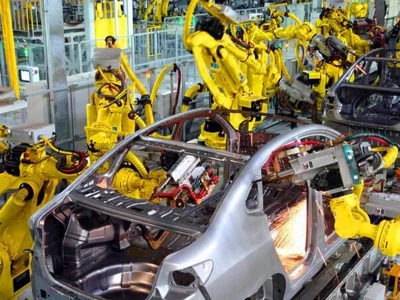
During the forecast period, laser welding machines are expected to significantly increase their market share in the automotive sector. Laser welding technology is used in various aspects of automotive manufacturing, including body structure components, white body welding, and laser lap welding of automotive panels. Laser welding has no adverse impact on the appearance and quality of parts, effectively suppressing deformations and embrittlement issues, resulting in strong and durable welds. It reduces the need for filler materials, lowering the risk of welding defects and making it a safer choice for automotive applications. Additionally, laser welding is gaining attention for its applications in the field of new energy vehicles and power battery manufacturing, as these industries require efficient, precise, and sustainable welding techniques.
Laser Welding in the Semiconductor Sector
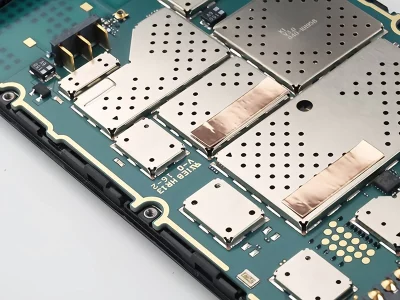
As the semiconductor industry continues to expand, the demand for semiconductor manufacturing increases, along with higher process requirements. Laser micro-welding technology is employed for welding small components and materials, including precise welding of parts smaller than 2 millimeters. In integrated circuit design and manufacturing, laser micro-welding technology facilitates data packaging on circuit boards, wire bonding to printed circuits, silicon plate welding, fine wire bonding to integrated control circuits, and more. Compared to traditional welding methods, laser micro-welding technology offers clear advantages, allowing access to and processing in areas that were previously unreachable by other Chinese traditional welding methods. It can also be applied to welding various materials, and laser welding point accuracy far surpasses that of traditional welding methods.
Continued Growth in Welding Robot Applications
Presently, a crucial direction in the laser welding industry is the extensive application of laser welding robots for welding and bonding tasks. Laser welding robots typically consist of multi-axis robotic arms with laser cutting heads. They offer high-speed operation, excellent weld quality, automation, and precision. In the automotive manufacturing sector, laser welding robots are widely used for connecting components such as car frames, doors, and engine hoods. They are also employed for automated production of car body outer panel welding, enhancing welding quality and efficiency while reducing labor costs. In the electronics manufacturing sector, laser welding robots are used for welding components like battery cells and circuit boards, ensuring the quality and reliability of electronic components while meeting the demand for precise connections in the manufacturing of microelectronic devices.
Technological Advancements in Plastic Laser Welding Equipment
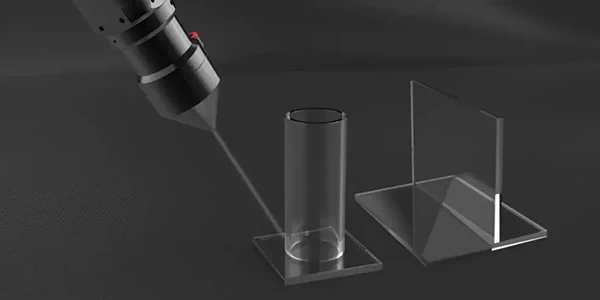
In recent years, the adoption of plastic products in the healthcare sector has simplified operations and promoted the introduction of innovative processes and technologies, driving continuous improvements in plastic joining and welding techniques by medical device manufacturers. Innovations include servo-driven ultrasonic welding machines and the emergence of 2μm lasers in the field of transparent plastic welding. It’s worth noting that laser welding technology not only enhances processing efficiency and accuracy but also eliminates the need for harmful adhesives and solvents, highlighting its environmental benefits.
Laser Hybrid Welding and 3D Printing
Laser hybrid welding is an advanced technology that combines the advantages of laser welding and arc welding, resulting in improved welding speed and quality. This method finds widespread applications in large structures, aerospace, shipbuilding, and more. Furthermore, the integration of laser welding with 3D printing technology allows manufacturers to produce complex three-dimensional parts, from aerospace engine components to medical implants. This fusion of technologies provides limitless potential for future manufacturing and design.
Green and Environmentally Friendly Practices
Green welding practices are a significant trend in the future market. Laser welding is considered more environmentally friendly than traditional welding methods, as it eliminates the need for harmful welding gases and solvents. Additionally, laser welding technology reduces scrap rates, lowers resource wastage, and helps reduce environmental impacts. This sustainable trend makes more companies opt for laser welding as part of their production processes.
Potential of the Asia-Pacific Laser Welding Machine Market
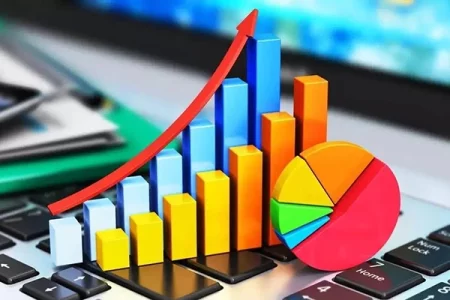
By 2027, the laser welding machine market in the Asia-Pacific region is projected to grow by 52%. The Asia-Pacific region is currently becoming a vital center for automobile production and sales, attracting the attention of numerous global automotive manufacturers seeking to establish manufacturing bases or source raw materials from the region. The establishment of new manufacturing facilities across Asia and the development of laser welding technology have a positive impact on the region’s automotive and laser welding market, offering significant opportunities for growth.
In Conclusion
In summary, the laser welding market is showing strong growth trends, driven by ongoing technological advancements and widespread applications. In the future, the market will continue to benefit from industries like automotive manufacturing, electronics manufacturing, medical devices, and more. Additionally, it will be influenced by cutting-edge technologies such as laser hybrid welding, 3D printing, intelligent automation, and environmentally friendly practices, providing more opportunities for innovation and efficiency improvements in the manufacturing industry.