Table of Contents
With the continuous development of manufacturing technology, laser cutting technology has been widely applied in industrial production as an efficient and precise processing method. However, to achieve superior laser cutting results, it is essential to comprehensively consider and rationally control multiple factors. This article will delve into various factors affecting laser cutting effects, including laser output power, laser output mode, focal point position, laser cutting speed, cutting material, auxiliary gas pressure, and more.
Laser Output Power
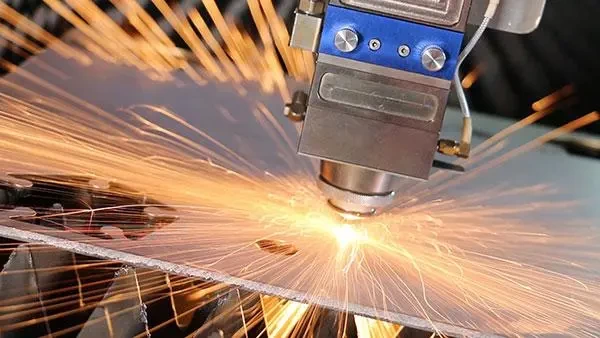
The required power for laser cutting is determined by the material’s characteristics and the cutting mechanism. Materials with high surface reflectivity, good thermal conductivity, or higher melting points demand larger laser power and power density. Different cutting mechanisms for the same material may require varying power levels. Vaporization cutting requires the highest power, followed by melting cutting, and the lowest power is needed for oxygen-assisted melting cutting. As the thickness of the sheet increases, the required laser power also increases.
Laser Output Mode
The laser beam quality is categorized into single-mode and multi-mode, where single-mode has a concentrated energy density at a single point, while multi-mode has two or more concentrated points. In cutting applications, the focus spot significantly influences the quality of the cut. Single-mode lasers with finer cores have superior beam quality compared to multi-mode lasers, which exhibit a Gaussian distribution of energy, forming a peak resembling a sharp, circular mountain. Multi-mode lasers have a coarser core and lower beam quality, forming an inverted cup-shaped 3D image with steeper edges.
Single-mode excels in thin sheets, while multi-mode performs better in thick sheets. However, comparing single-mode and multi-mode is not of intrinsic value; they are configurations of fiber laser systems. It’s akin to choosing between a sedan and an off-road vehicle, where the selection depends on the specific processing needs of end-users.
Focal Point Position
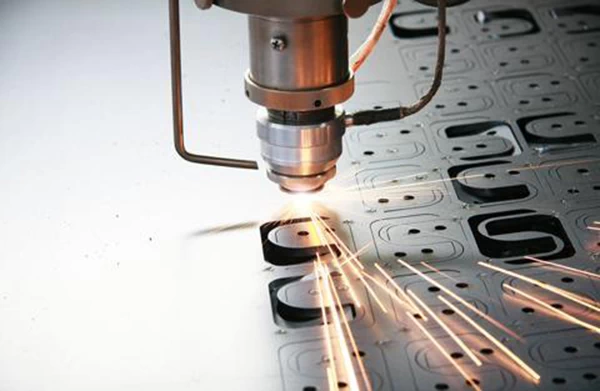
The relative position of the focal point to the workpiece surface is crucial for ensuring cutting quality. Typically, the focus position is either just at the workpiece surface or slightly below it during cutting. Maintaining a constant relative position between the focus and workpiece throughout the cutting process is vital for stable cutting quality. Optimal cutting results, with smaller kerfs and higher efficiency, are achieved when the focus is in the preferred position, often just below the nozzle. The distance between the nozzle and the workpiece surface is generally around 1.5mm.
The size of the focused laser beam spot is directly proportional to the focal length of the lens. A short-focal-length lens results in a small spot size with high power density at the focus, beneficial for cutting materials. However, the drawback is a short focal depth with limited adjustment margin, making it suitable for high-speed cutting of thin materials. In contrast, a long-focal-length lens provides a broader focal depth, sufficient power density, and is suitable for cutting thick workpieces.
Laser Cutting Speed
In laser cutting, the cutting speed significantly affects the quality of the cut material. Ideally, a cutting speed that produces smooth lines on the cut surface without molten slag underneath is desired. When the auxiliary gas pressure and laser power are constant, the cutting speed exhibits a nonlinear inverse relationship with the kerf width. Slow cutting speeds result in prolonged laser energy action on the kerf, leading to increased kerf width. Excessively slow speeds create a significant disparity between the upper and lower kerfs, resulting in reduced cut quality and a substantial decrease in production efficiency.
As the cutting speed of a metal laser cutting machine increases, the laser beam’s action time on the workpiece decreases. This reduces heat diffusion and thermal conduction effects, resulting in a corresponding reduction in kerf width. However, excessively high speeds may lead to incomplete cutting due to insufficient input of cutting heat, causing the material to remain uncut. This incomplete cutting phenomenon, combined with the failure to blow away melted material promptly, results in the re-welding of the kerf.
Cutting Material
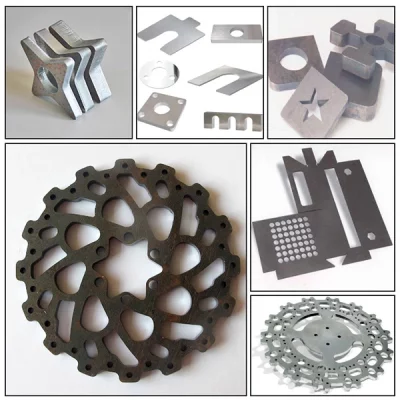
The following factors have the greatest impact, or even determine whether laser cutting is possible, on laser cutting quality:
Material Surface Reflectance
Non-metallic materials generally absorb well for 10.6mm far-infrared beams emitted by CO2 lasers, exhibiting high absorption rates. Metallic materials with high reflectivity, such as gold, silver, copper, and aluminum, are generally unsuitable for CO2 laser beams, especially continuous-wave beams, for cutting.
For aluminum and copper metals, a starting power of at least 3kW is usually required to create the initial small hole needed for penetration. Materials like steel, nickel, and titanium exhibit some absorption of the 10.6mm CO2 beam, especially when the material surface is heated to a certain temperature or has an oxide film, resulting in significantly improved absorption rates and better cutting effects.
For opaque materials, absorption rate = (1 – reflectance), which depends on the material surface treatment status, temperature, and wavelength. The material’s absorption rate plays a crucial role in the initial heating stage, but once small holes form inside the workpiece, the blackbody effect of the holes makes the material’s absorption rate close to 100%.
Material Surface Condition
The surface condition of the material directly affects the beam absorption, especially surface roughness and surface oxide layers, causing noticeable changes in surface absorption rates. In laser cutting practice, the impact of the material’s surface condition on beam absorption rates is sometimes utilized to improve cutting performance.
Auxiliary Gas Pressure

During laser cutting, the auxiliary gas pressure plays roles such as blowing away molten slag, cooling the material, and assisting combustion. Auxiliary gases include oxygen, compressed air, nitrogen, and inert gases.
Oxygen can participate in metal combustion, improving cutting efficiency, and is suitable for cutting most metals. Inert gases and air are suitable for cutting some metal materials (such as aluminum alloys) and non-metallic materials, preventing material combustion.
Yupec Laser reminds you that if the auxiliary gas pressure is too high, vortexes may appear on the material surface, weakening the ability to remove molten material and causing an increase in kerf width and rough cutting surfaces. If the pressure is too low, molten material cannot be completely blown away, leading to material adherence and slag attachment on the lower surface.
Therefore, it is essential to adjust the auxiliary gas pressure during cutting to achieve the best cutting quality.
Laser Nozzle
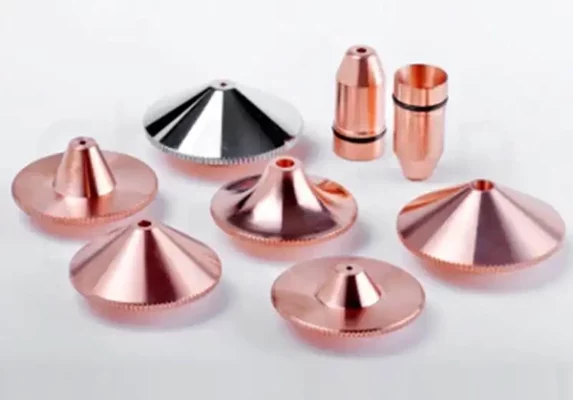
The laser nozzle is a crucial component that affects laser cutting quality and efficiency. Improper selection or poor maintenance of the nozzle can cause contamination or damage. Irregularities in the roundness of the nozzle or local blockages due to thermal metal spattering can lead to vortex formation in the nozzle, significantly degrading cutting performance. Sometimes, misalignment between the nozzle opening and the focused laser beam axis can shear the beam at the nozzle’s edge, affecting cut quality, increasing kerf width, and causing cutting dimensions to shift.
Two critical aspects should be considered for nozzles:
- Influence of Nozzle Diameter
- Influence of Nozzle-to-Workpiece Surface Distance
Optical Path System
The original laser beam emitted by the laser is transmitted through the optical path system (including reflection and transmission) with extremely high power density, accurately illuminating the workpiece surface. Regular inspection and timely adjustment of optical components in the optical path system are necessary to ensure that when the cutting torch runs above the workpiece, the beam is correctly transmitted to the center of the lens and focused into a small spot, enabling high-quality cutting. Any changes or contamination of optical components can affect cutting quality and even cause cutting to be impossible.
Contaminants in the airflow and spatter sticking to the optical path lenses or insufficient lens cooling can cause overheating of the lenses, affecting beam energy transmission. This can lead to drift in optical alignment, resulting in serious consequences. Overheating of the lens can cause focal point distortion and even jeopardize the lens itself.
Conclusion
The factors influencing the cutting quality and efficiency of laser cutting machines include laser output power, output mode, focal point position, cutting speed, cutting material, auxiliary gas pressure, nozzle, and the optical path system. To achieve excellent cutting results, it is necessary to consider these factors comprehensively and implement precise control. In the future, with technological innovation, laser cutting will witness more efficient and intelligent solutions, bringing new opportunities for the manufacturing industry. Through in-depth understanding and continuous efforts, we can fully unleash the potential of laser cutting technology, providing reliable and efficient solutions for precision machining.