Table of Contents
High-power laser cutting is a cutting-edge manufacturing process that utilizes a high-energy density laser beam to precisely and efficiently cut through various materials. Unlike traditional cutting methods that may involve physical contact with the material or mechanical tools, high-power laser cutting employs a focused laser beam to generate intense heat at the cutting point, effectively vaporizing, melting, or ablating the material.
Advantages of High-power Laser Cutting
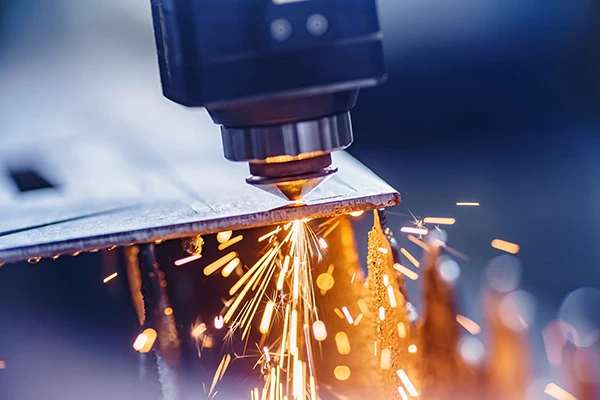
High Cutting Quality
The focused laser beam enables extremely precise and clean cuts, resulting in high-quality finished products with minimal distortion, burrs, or rough edges. This makes high-power laser cutting ideal for applications where precision and finish are paramount.
High Efficiency
High-power laser cutting machine offers rapid cutting speeds and high processing efficiency compared to conventional cutting equipment. The concentrated energy of the laser beam allows for swift material removal, making it a cost-effective solution for industrial manufacturing processes.
Non-contact Cutting
Unlike mechanical cutting methods which involve physical contact between cutting tools and the material, high-power laser cutting is a non-contact process. This eliminates the risk of tool wear, contamination, or damage to delicate materials, and allows for cutting intricate shapes without the need for additional tooling.
Various Materials
High-power laser cutting is versatile and can be applied to a wide range of metals, such as steel, aluminum, and titanium, copper, and more. This versatility makes it a preferred choice across industries spanning automotive, aerospace, electronics, medical devices, and beyond.
Adaptability and Flexibility
Overall, high-power laser cutting technology represents a cutting-edge solution for precision manufacturing, offering superior cutting quality, efficiency, versatility, and adaptability across a wide range of industries and applications.
Common Defects and Solutions in High-power Laser Cutting
In general, important process parameters that affect the quality of the cutting quality include cutting speed, laser power, auxiliary gas, focus position, laser nozzles, and material properties. It can be seen that there are many factors affecting the laser cutting process. If the control is improper or the parameters are not accurate, the cutting precision and cutting quality will have a great impact.
Let’s take a look at the common cutting defects and solutions in daily processing.
1. When cutting carbon steel with oxygen, some common issues may include:
1.1 The striping on the upper layer and the drag lines on the lower layer of the sheet metal are both excessively rough.
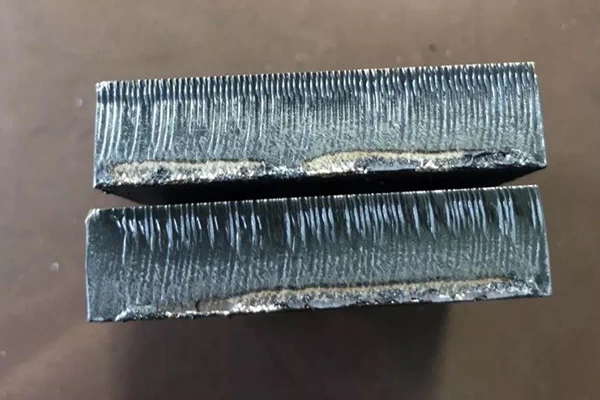
Possible Reason:
- Nozzle selection is too big;
- Excessive cutting pressure causes over-burning;
- The cutting speed is too slow, causing excessive burning or too fast, resulting in insufficient cutting.
Solution
- Replace small nozzle with suitable nozzle;
- Reduce the air pressure to have a brighter face of the cutting edge;
- Adjust the cutting speed to a suitable range for the current power.
1.2 The upper layer of the sheet metal shows slightly rough striping, with minor or deeper serrations, while the lower layer exhibits better drag lines.
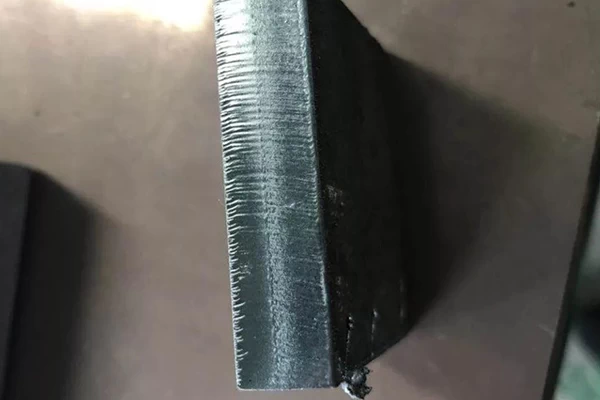
Possible Reason:
- Nozzle selection is too large;
- The defocus amount does not match;
- Slower cutting speed.
Solution
- Replace small nozzle with suitable nozzle;
- With the nozzle diameter unchanged, continue to increase positive defocus;
- Adjust the cutting speed to a range suitable for the current power.
1.3 The upper layer of the sheet metal section shows good striping, but there is slag hanging at the bottom, which affects the section’s quality.
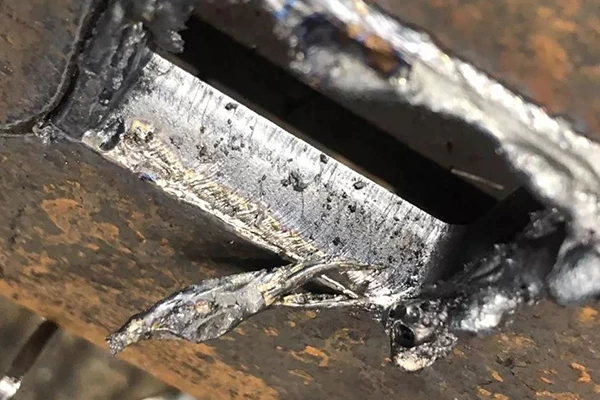
Possible Reason:
- The forward defocus is too large, causing the energy to be concentrated and forming a lagging tail;
- Air pressure feed error: Too small air pressure causes cutting tail to form drag line lag and slag;
- Too fast cutting speed leads to lag.
Solution
- Reduce forward defocus appropriately, the remaining parameters remain unchanged, observe the slagging situation at the bottom;
- Increase the feed air pressure appropriately, try to increase it to about 1Bar at most, and observe the situation;
- Adjust the cutting speed to a range suitable for the current power.
2. When cutting stainless steel with nitrogen, some common issues may include:
2.1 When cutting thin stainless steel sheets, delamination and rough cutting surfaces may occur
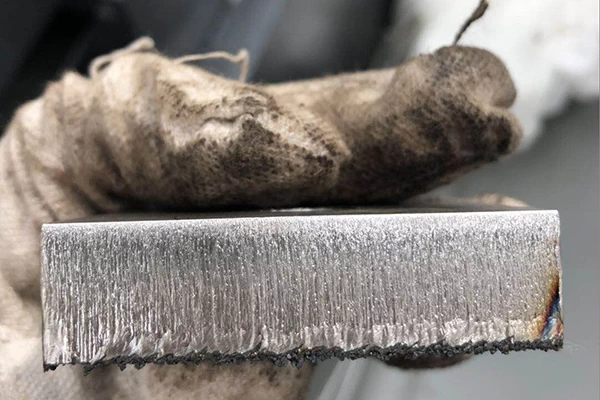
Possible Reason:
- The negative defocus amount is too large, resulting in plasma generation, blue light generation and layering;
- Nozzle diameter is too small;
- Air pressure feed is too large.
Solution
- Reduce negative defocus, the remaining parameters remain unchanged, observe the phenomenon;
- Replace the nozzles of the larger size;
- Reduce air pressure feed appropriately.
2.2 When cutting thick stainless steel plates, encountering incomplete cuts. The cutting section does not reach the bottom of the plate.
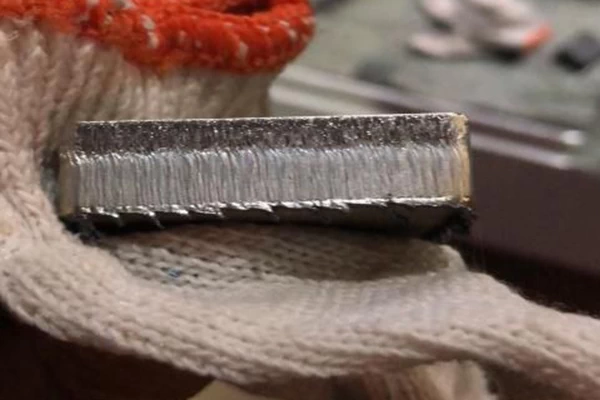
Possible Reason:
- The nozzle selection is too small;
- Defocus amount mismatch;
- Insufficient gas pressure, resulting in insufficient cutting.
Solution
- Replace larger nozzles to increase gas flow;
- Continue to increase negative defocus to make the cutting section reach the bottom;
- Increase air pressure.
2.3 Encountering delamination during the cutting of thick stainless steel plates, adjusting the air pressure and positive / negative focus amounts does not yield significant improvement in the outcome.
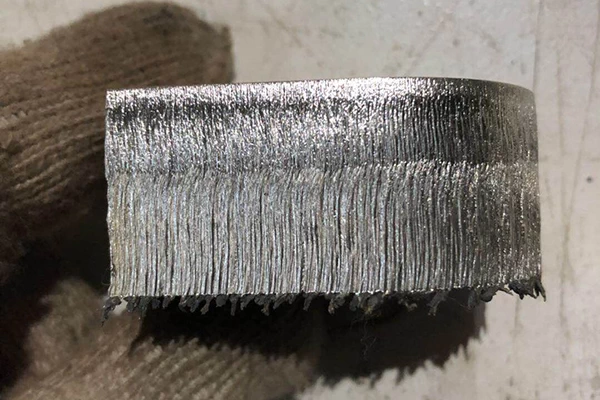
Possible Reason:
- When the speed cannot be increased, the laser energy is too concentrated and the reaction with the material is too violent;
- The nozzle selection diameter is too small, resulting in too little flow.
Solution
- Under the condition that the peak power is constant, reduce the frequency and the duty cycle appropriately.
- Replace larger nozzles to increase gas flow.