Table of Contents
In today’s daily life, cars have become an indispensable mode of transportation. Whether in terms of performance, features, engines, or chassis, the safety of a vehicle is always one of the factors to consider. Only when a vehicle’s safety meets the requirements from various dimensions can you drive more comfortably and freely.
Laser welding technology is characterized by high welding process efficiency and flexibility. In the process of automobile manufacturing, it can be used for welding the car body and various automotive components, reducing the overall weight of the car body, improving the body assembly precision, and meeting the demands for lightweight and improved safety performance in automobile manufacturing. Additionally, it can also reduce assembly and stamping costs in car manufacturing and enhance the integration of the vehicle body. Therefore, how to actively and effectively apply laser welding technology has become a crucial consideration for today’s automotive manufacturing companies. The following will provide a detailed discussion of the application of laser welding technology.
Advantages of Hot-Formed High-Strength Steel
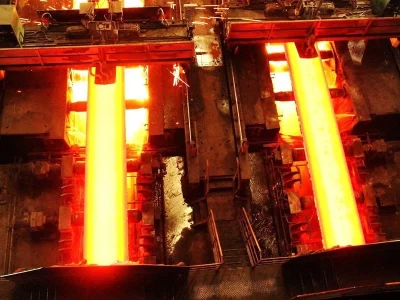
In pursuit of lightweight and improved safety, automobile manufacturers extensively utilize hot-formed high-strength steel as a primary material for automotive components. Hot-formed high-strength steel possesses exceptionally high strength, enhancing the vehicle’s safety and improving stamping formability. It is commonly used in critical areas of the car body, such as door impact beams, front and rear bumpers, A/B pillars, central channels, upper and lower firewalls, and more. These hot-formed steels encase the passenger cabin in a sturdy cage, making the vehicle less prone to deformation in the event of a collision, thereby better protecting the occupants’ safety. Generally, the more advanced the car, the more hot-formed steel is used, resulting in a stronger body structure.
Challenges in Welding Hot-Formed High-Strength Steel

High-strength steel, after undergoing a series of hot forming processes, becomes more challenging to cut. Moreover, it is equipped with an aluminum-silicon coating on its surface, enhancing corrosion resistance for the components. However, this coating is highly detrimental to the welding process, as it has very poor electrical conductivity. Traditional resistance spot welding relies on melting the welding position of the parts to permanently bond the atoms together.
Due to the complexity of the resistance spot welding process, factors such as material, parameters, and process-related elements intertwine, posing certain difficulties in quality control. The extensive use of hot-formed components also exposes process flaws, especially issues like welding spatter and burrs, which significantly impact the appearance and production efficiency of the welds. Addressing these problems is crucial to improve welding performance and ensure weld quality.
Laser Welding in Automotive Applications
The automotive manufacturing industry employs a wide range of welding techniques, including laser welding, MAG welding, resistance welding, MIGTIGCO welding, and others. However, due to variations in sheet metal thickness and the complexity of jointing, laser welding technology is often the preferred choice.
Laser welding can be further divided into high thermal melt-through laser welding and heat conduction melt-through welding, depending on the penetration power of the laser beam. Melt-through material welding technology allows for more thorough internal melting of the welded material. Heat conduction material welding technology utilizes a high-temperature effect generated through heat conduction, achieving the welding process.
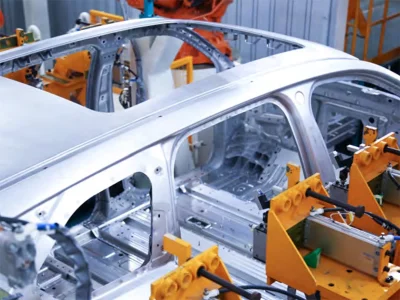
Body Welding
Laser welding in the automotive industry is mainly used in the assembly and connection of body-stamping parts, including the welding of car roofs, trunk lids, and frames. Another essential application is body laser welding, focusing on the structural components of the body, including doors, body side frame structures, pillars, and more. Laser welding enhances the body's strength, addressing the challenges of conventional resistance spot welding. For complex welding of the overall internal structure of the vehicle, such as the entire welding of the vehicle roof to the body chassis, new technologies like micro-laser integral welding have been adopted, increasing the body's rigidity and reducing production costs.
Laser-Welded Uneven Thickness Plates
The use of laser-welded uneven thickness plates in car body manufacturing reduces weight, lowers the number of components, improves safety and reliability, and lowers production costs. However, this approach imposes strict demands on the welding process.
Gear and Transmission Component Welding
Various parts of the gearbox can be welded using laser welding machines, especially components such as the differential housing and drive axles in passenger car gearboxes. Typically, individual parts are produced separately and then joined and welded together.
Characteristics of Laser Welding in Automotive Body
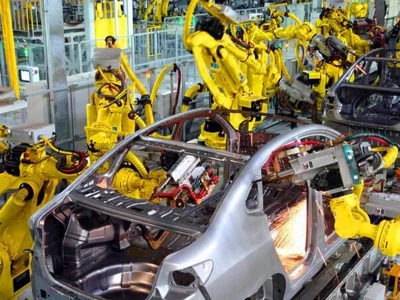
Non-Contact Processing
The most significant advantage of laser welding in automobile manufacturing lies in its advanced non-contact processing. Traditional methods, such as screw fastening and adhesive bonding, fail to meet the modern automotive industry's requirements for precision and robustness. Moreover, the application of new materials has diminished the competitiveness of conventional processing methods. Laser welding is non-contact, enabling precise welding without touching the product. It represents a significant leap forward in terms of connection strength, seamlessness, precision, and cleanliness, offering more possibilities for advancing automotive technology.
Laser Welding Enhances Automobile Lightweighting
The use of laser welding in automotive manufacturing allows for the replacement of more cast components with stamped parts and dispenses with scattered spot welds, thus reducing overlap width and some reinforcement components. This leads to a reduction in the vehicle's structural volume and, subsequently, weight reduction, meeting the demands of energy efficiency and emissions reduction in automotive manufacturing.
Improved Body Assembly Precision and Rigidity
A car body consists of hundreds, if not thousands, of different parts, and how these parts are interconnected directly affects the vehicle's structural rigidity. Laser welding can connect metal materials of varying thicknesses, brands, types, and grades, greatly improving welding precision and body assembly precision. This results in more than a 30% increase in body rigidity, thus enhancing vehicle safety.
Laser Hybrid Welding Enhances Process Stability
Compared to pure laser welding technology, laser hybrid welding significantly enhances the ability to join sheet metal parts and takes full advantage of the process stability during high-speed laser welding with arc welding. Additionally, the use of laser welding can reduce stamping and assembly costs in the automotive body manufacturing process, shorten production cycles, reduce the number of parts, and increase the overall integration of the vehicle body.
YUPEC Advanced Laser Welding Solutions for Automobile Manufacturing
In the automotive manufacturing industry, YUPEC Company stands as a leader with its outstanding technology and comprehensive solutions.
YUPEC’s Laser Welding System for Battery Tray is specifically designed for electric vehicle battery trays, capable of achieving high precision and efficiency in welding, ensuring the stability and safety of the battery trays.
YUPEC’s Laser Punching and Welding Integrated System can achieve rapid punching and welding of bumpers, greatly improving production efficiency and product quality.
Integrating robot technology, YUPEC’s Robot Flexible Laser Cutting and Welding System realizes highly automated and flexible laser cutting and welding, applicable to the manufacturing of parts with various complex structures.
The Line Pipe Laser Welding Connection System from YUPEC provides efficient and high-quality laser welding solutions for automotive line pipes, ensuring their stability and durability.
Integrating CNC technology, the JKA FlexiWeld-Cut Pro series achieves high precision and efficiency in laser welding, widely used in the manufacturing of precision parts.
The Auto-Welding Production Line series offers a fully automatic welding production line, achieving efficient and high-quality production, meeting the large-scale production needs of automotive transmission parts.
Conclusion
Today, the application of laser welding in automotive body production is a growing trend. Laser welding technology has had a profound impact on traditional automotive welding processes, and major automakers are embracing it enthusiastically. Adopting new technology translates to greater competitiveness, and in the increasingly competitive market, competitiveness translates to market share.
The significant economic value of laser welding is highly appealing to automotive companies. In the future, laser welding technology will have ample room for development in automotive manufacturing, gradually replacing traditional welding processes for body welding. High levels of automation and intelligence in production lines are driving automakers to replace traditional welding processes and transition to fully automated manufacturing. Laser welding is not limited to structural component welding but, with improving technology and the use of high-precision inspection instruments, will gradually be applied to the manufacturing of body panels. This reduces the cost of developing molds and the investment costs for automakers, creating more economic value for the industry.